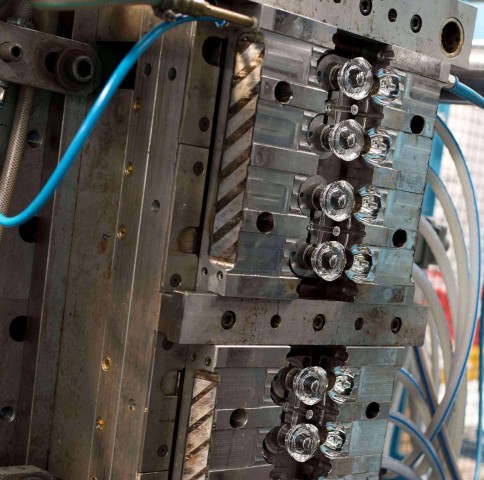
Injection moulding is one of the techniques of moulding plastics. This method is used to manufacture a range of shipping containers, packaging for industry, cosmetic products, household chemicals, as well as different types of closures, for example for PET bottles or perfumes. Why is injection moulding a good method for creating product packaging?
What does injection moulding consist in?
Injection moulding makes creating plastic packaging for various uses and in different forms possible. The injection method can be used to create containers and lids for foodstuffs, interestingly designed packaging for body care, and even packaging for household chemicals and goods.
Injection moulding consists in injecting plasticised material into an injection mould where it then solidifies. The plastics used in this process are in the form of granules. However, there are also other forms of processing for this material, which use prepolymers and agents that polymerise in the course of the moulding process. This method of injection moulding is called reaction injection moulding (RIM).
Injection moulders are essential in creating plastic packaging. They can be used for moulding thermoplastic and thermosetting materials.
Injection moulded plastic packaging – manufacturing process
The first stage in the process of moulding plastic packaging with injection is heating and melting the material. It is dosed from a container by means of a specially designed screw revolving inside a cylinder, which is then heated by the heating elements. The temperature of the plastic increases as a result of friction on the cylinder walls. Owing to the rotational motion, the heat is evenly distributed around the cylinder and the high pressure within the screw fosters the plastic to form.
The next stage in manufacturing injection moulded plastic packaging is the actual injection. The screw here moves in a rotational motion, but also in a reciprocating motion, which results in the molten plastic flowing over into the prepared injection mould. The injection mould is most often made of steel and its design allows it to become filled quickly, which favours effectiveness in the process of manufacturing packaging.
Depending on the type of plastic used to manufacture the packaging, it is cooled or heated once it is poured into the form. Thermosetting plastics require heating and the thermoplastic ones require cooling. With the use of an appropriate method of stabilisation for the plastic, it maintains the shape of the mould when it cools down.
Then the mould is emptied by means of automatic ejection. Ready packaging is cleaned of plastic residues, which may solidified in the feeding channels or on the parts connecting the two halves of the mould. This is conducted by mechanically cutting unnecessary elements, as well as by means of polishing the packaging.
Packaging we can manufacture by means of injection moulding includes:
* plastic shipping containers,
* industrial packaging (paint or foodstuff buckets),
* thin-walled injection packaging (containers for ice cream, margarine, cups for milk products),
* injection moulded boxes and jars for packing cosmetic and pharmaceutical products, as well as household chemicals.
The technology of injection moulding also allows us to create closures for different types of packaging.
PET bottles – injection blow moulding
We can also use the injection moulding technology to manufacture PET bottles. They are moulded by means of two methods. The single-stage ISBM is also referred to as injection blow moulding. The single-stage method makes it possible to conduct the production process in a single machine, resulting in a much faster and more efficient process. The clear advantage of this method is higher visual quality of the product in comparison to other methods. Through this method, packaging in non-standard shapes (oval, decentralised) can be produced, which are often used for example in the cosmetic industry.
Powrót do listy artykułów